Position:Home » Industry News
Resistors Classified by Materials
Writer:Microhm Page View:Date:2019-12-18
Resistors are produced with a wide variety of materials and manufacturing processes. Each resistor material has its typical properties and specific areas of use. The main types that are used in electrical engineering are summed below.
Wirewound Resistor
These types are made by winding resistance wire in a spiral around a non-conductive core. The resistance wire is usually a nickel-chromium alloy and the core is often ceramic or fiberglass. A coating such as vitreous enamel is used for protection. The spiral winding has capacitive and inductive effects that makes it not suitable for applications higher than 50 kHz. Often other winding techniques are used to reduce the undesired high frequency effects. Wirewound resistors are essentially produced for high precision or for high power applications. They have low noise, are robust, and are temperature stable. Resistance values are available from 0.1 up to 100 kW, with accuracies between 0.001 and 20%. Microhm Electronics' wirewound resistors, especillay metal clad NUAL series are popular wire wound resistors for high power application.
Foil Resistor
The foil resistor was invented in the 1960’s and is still the most accurate and stable type today. The resistive element is a thin bulk metal foil that is cemented on a ceramic substrate. The foil thickness is several micrometers. Inherent to the mechanical design, they feature a very low temperature coefficient of resistance. They are used for applications with high precision requirements. MVR2321-4 is a typical metal foil resistor especially suitable for precision measurement.
Carbon Film
A thin, pure carbon film is deposited on an insulating cylindrical core. A spiral cut is made in the film to increase the resistive path. This increases the resistance value and is also a way to control the resistance value more precise. Values from 1Ω up to 10 M Ω are available. The accuracy is a significant improvement compared to carbon composition, but metal and metal oxide film have overall better properties and gained therefore more popularity. In applications that require high pulse stability, special carbon film resistors are used.
Metal Film
Metal film resistors are usually made of Nichrome, but also other materials such as tantalum nitride is used. The resistive film is printed on a cylindrical or flat insulating substrate. The resistive material is a combination of a Ceramic material and a Metal, and therefore these resistors are also referred to as Cermet. Just as with carbon film, the resistance value is adjusted by cutting a spiral pattern in the film. This can be done with an abrasive or a laser. The stability, temperature coefficient and tolerance are better than for carbon film. Typical tolerances are between 0.5% and 2% with a temperature coefficient between 50 and 100 ppm/K. Stability is lower than for wirewound, but the high frequency properties are better. HPMRY series and PMRY series are welllkown for their low TCR, high precision and competitive price.
Metal Oxide Film
They are similar to metal film with the difference that the resistive material is a metal oxide, such as tin oxide. These durable resistors feature a better reliability and stability than metal film resistors. Furthermore the operating temperature is higher. Therefore they are more used in applications requiring a high endurance.
Wirewound Resistor
These types are made by winding resistance wire in a spiral around a non-conductive core. The resistance wire is usually a nickel-chromium alloy and the core is often ceramic or fiberglass. A coating such as vitreous enamel is used for protection. The spiral winding has capacitive and inductive effects that makes it not suitable for applications higher than 50 kHz. Often other winding techniques are used to reduce the undesired high frequency effects. Wirewound resistors are essentially produced for high precision or for high power applications. They have low noise, are robust, and are temperature stable. Resistance values are available from 0.1 up to 100 kW, with accuracies between 0.001 and 20%. Microhm Electronics' wirewound resistors, especillay metal clad NUAL series are popular wire wound resistors for high power application.
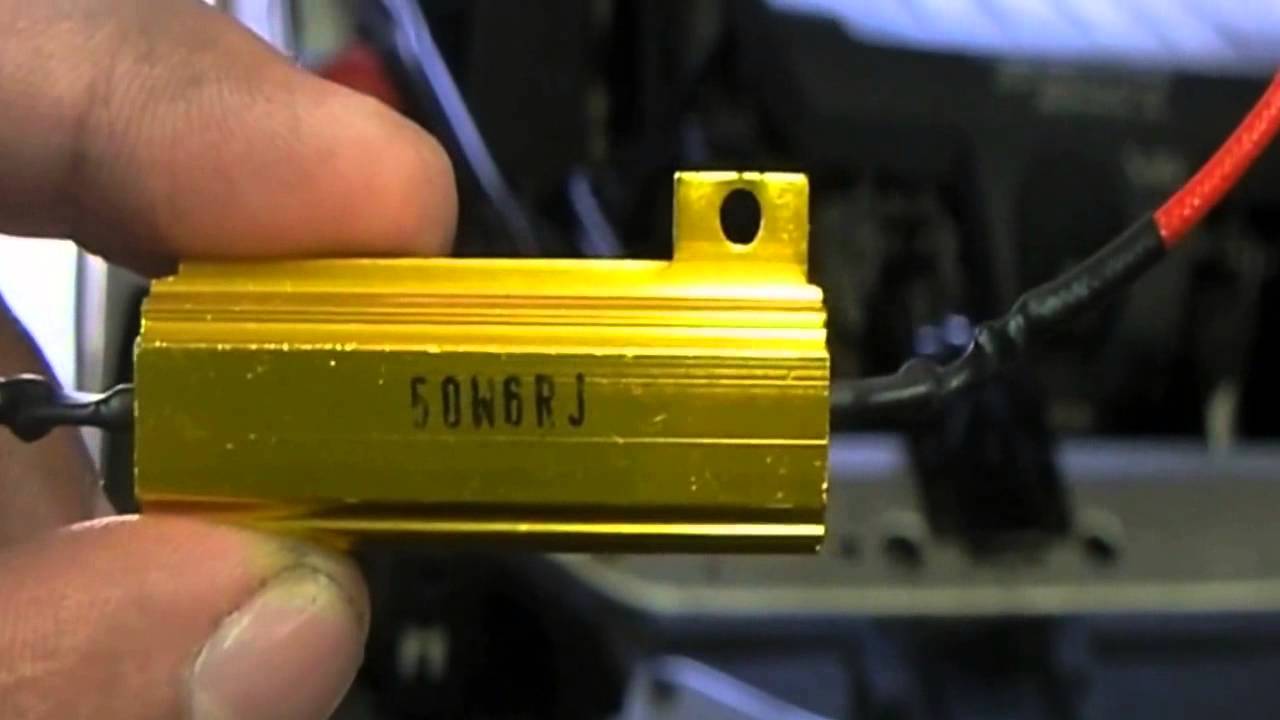
Foil Resistor
The foil resistor was invented in the 1960’s and is still the most accurate and stable type today. The resistive element is a thin bulk metal foil that is cemented on a ceramic substrate. The foil thickness is several micrometers. Inherent to the mechanical design, they feature a very low temperature coefficient of resistance. They are used for applications with high precision requirements. MVR2321-4 is a typical metal foil resistor especially suitable for precision measurement.
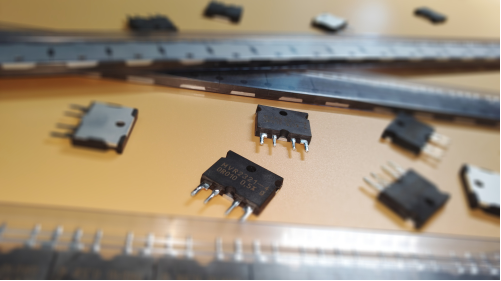
Carbon Film
A thin, pure carbon film is deposited on an insulating cylindrical core. A spiral cut is made in the film to increase the resistive path. This increases the resistance value and is also a way to control the resistance value more precise. Values from 1Ω up to 10 M Ω are available. The accuracy is a significant improvement compared to carbon composition, but metal and metal oxide film have overall better properties and gained therefore more popularity. In applications that require high pulse stability, special carbon film resistors are used.
Metal Film
Metal film resistors are usually made of Nichrome, but also other materials such as tantalum nitride is used. The resistive film is printed on a cylindrical or flat insulating substrate. The resistive material is a combination of a Ceramic material and a Metal, and therefore these resistors are also referred to as Cermet. Just as with carbon film, the resistance value is adjusted by cutting a spiral pattern in the film. This can be done with an abrasive or a laser. The stability, temperature coefficient and tolerance are better than for carbon film. Typical tolerances are between 0.5% and 2% with a temperature coefficient between 50 and 100 ppm/K. Stability is lower than for wirewound, but the high frequency properties are better. HPMRY series and PMRY series are welllkown for their low TCR, high precision and competitive price.
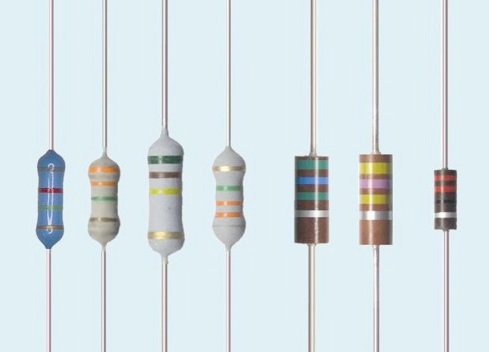
Metal Oxide Film
They are similar to metal film with the difference that the resistive material is a metal oxide, such as tin oxide. These durable resistors feature a better reliability and stability than metal film resistors. Furthermore the operating temperature is higher. Therefore they are more used in applications requiring a high endurance.
Keywords:
Latest News
- Resistor's role in measuring and correcting LED,,,
- Single through-hole resistors' characteristics ,,,
- Why shunt resistors for current sense applicati,,,
- Metal-film resistors with small size, high resi,,,
- 36W High-Current Shunt Resistors MMS8420,,,
- 1W Surface Mount Resistor MPR1206,,,
- An Overview of Microhm Electronics' Resistor Pr,,,
- More anti-sulfur resistors used in harsh envir,,,
- Resistance changes with temperature,,,
- 140W TO247 High Power Heatsinkable Resistor,,,
- MMS5930 is ideal for current sensing in industr,,,
- Shunt resistors selection for engineers' design,,,
- Considerations for choosing precision resistors,,,
- Ceramic Encased Cement Resistors NWH Series for,,,
- Resistors for Passive Balancing in Battery-Pow,,,
Hot Articles
- Microhm will take part in 10th Automotive World,,,
- Thanks for Visiting Microhm's Booth E5-5706 in ,,,
- Resistors in Short Supply: Blame Cars,,,
- New lunch: High Power Precision Shunt Resistor,,,,
- How to Test a Resistor,,,
- Innovative Technology, Future Electric: Electri,,,
- What is Precision Resistors?,,,
- SMD Resistors Sizes and Packages,,,
- The Construction and Features of Metal Film Res,,,
- What is a TO-220 Resisor?,,,
- Hot Selling Products: Precision Shunt Resistors,,,
- How to Calculate the Equivalent Resistance Valu,,,
- What is a Fixed Resistor?,,,
- Resistors in LED Circuits,,,
- Resistors Types and Materials Overview,,,
Resistance applications
- Why Zero-Ohm Resistors?,,,
- Miniature future for passive electronic compone,,,
- Heater Blower Motor Resistor in Air Conditioner,,,
- Urbanization Development Bringing the Transform,,,
- Difference Between High Precision Resistors and,,,
- Carbon Film Resistors' Features and Application,,,
- Precision Resistors' Construction and TCR,,,
- BMS for New Energy Vehicle,,,
- The Main Application for High Precision and Low,,,
- Surface Mount Resistor's Size and Package ,,,
- Industrial Roberts Applied to Solar Photovoltai,,,
- Shunt Resistor MMS8420 for High Current Stable ,,,
- The Measurement Accuracy of Automotive Shunt is,,,
- The Four Important Functions of Alloy Resistors,,,
- Select the Right Resistor for Harmonic Filterin,,,