The introduction of solar photovoltaic power to robots has become a bright spot in the industry. The use of robots can greatly improve the operation and maintenance effect of solar photovoltaic power stations, and reduce the operational errors of workers. In the aspect of efficiency, robot is superior to manual, which can effectively ensure the safe operation of photovoltaic power station. Well, the robots in photovoltaic power stations are mainly engaged in those photovoltaic power stations.
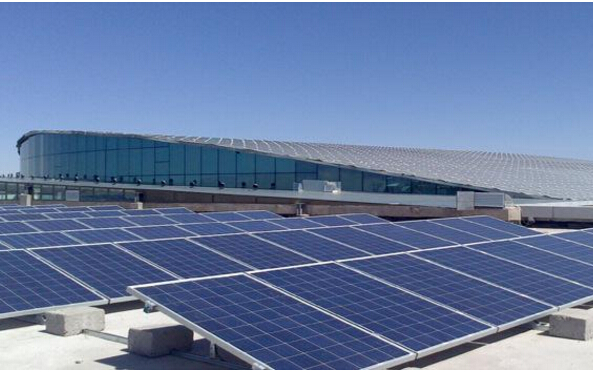
Firstly, the robot is responsible for measuring and classifying the power of solar modules.
At present, the robot using the sampling precision resistor to design has the very big enhancement in the performance, the sensitivity and the operation precision realizes the quality leap. At present, many robots hold photovoltaic modules close to the detection equipment, measure their output power and related parameters. Solar modules are labeled with output power, and the protection angle is installed. The robot grab modules and are neatly placed on the tray according to the classification requirements.
Secondly, the robot is responsible for the automatic cutting and framing of the solar power plant
With high-precision resistors, robots can operate freely in many cases, so robots are also well suited to solar panel assembly because they can quickly adapt to product conversion. After the photovoltaic module is laminated, the cutting tool is used to cut the edge of the photovoltaic module, and then the cutting edge is transferred to the frame robot workstation. A robot absorbs the photovoltaic module and puts it into the adhesive tape position for tape winding and sealing. After completion, the robot puts it into the framing machine. Another robot picks up the border and puts it in the frame. Then the framing machine is used to group the frame, and then the second robot absorbs it to the conveyor belt to work on the angle of pressing and filing. Next, a multitasking robot adheres to the junction box on the photovoltaic module, and a robot equipped with an inductive welding joint completes the welding work.
At present, the robot using the sampling precision resistor to design has the very big enhancement in the performance, the sensitivity and the operation precision realizes the quality leap. At present, many robots hold photovoltaic modules close to the detection equipment, measure their output power and related parameters. Solar modules are labeled with output power, and the protection angle is installed. The robot grab modules and are neatly placed on the tray according to the classification requirements.
Secondly, the robot is responsible for the automatic cutting and framing of the solar power plant
With high-precision resistors, robots can operate freely in many cases, so robots are also well suited to solar panel assembly because they can quickly adapt to product conversion. After the photovoltaic module is laminated, the cutting tool is used to cut the edge of the photovoltaic module, and then the cutting edge is transferred to the frame robot workstation. A robot absorbs the photovoltaic module and puts it into the adhesive tape position for tape winding and sealing. After completion, the robot puts it into the framing machine. Another robot picks up the border and puts it in the frame. Then the framing machine is used to group the frame, and then the second robot absorbs it to the conveyor belt to work on the angle of pressing and filing. Next, a multitasking robot adheres to the junction box on the photovoltaic module, and a robot equipped with an inductive welding joint completes the welding work.
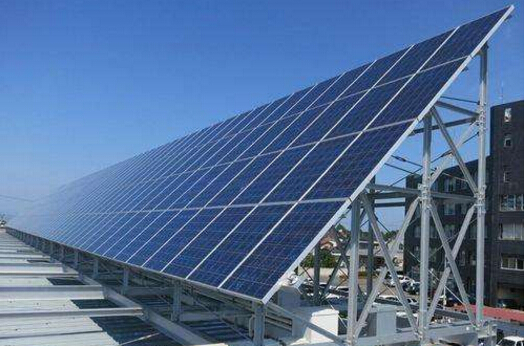
Thirdly, maintenance of solar power plants by robots 24 hours a day
The technology capability, the innovative idea and the overall strength of the robot have achieved a high level of product quality, not only meeting the requirements of the production of the photovoltaic industry, but also greatly improving the production efficiency. Only a very small amount of maintenance work is required for the robot, and the maximum availability can be achieved. No matter what kind of operation, the robot can complete the task in strict accordance with the requirements, and in any production link, it is a single and tireless “skilled worker”. It is worth mentioning that the robot has the function of customization, and the need of various processing tasks can be easily met without complex secondary development. Even if there is a change in production demand in the future, it is usually only necessary to re-program the robot, so it can continue to be put into use.
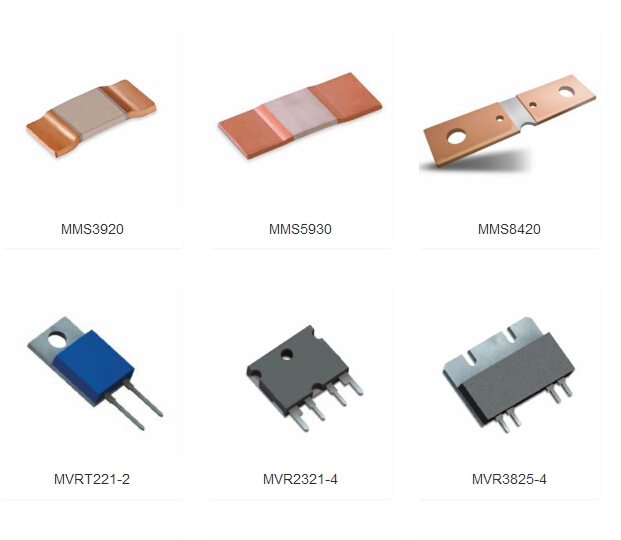
In general, robots using high-precision resistors are increasingly able to shorten production cycles, reduce costs, improve production, improve quality, significantly reduce medical compensation and scrap rates, and enhance market competitiveness. These ultra-high speed robots are equipped with machine vision and are excellent at taking and placing randomly placed batteries from a moving conveyor belt. Heavy-loaded robots are best suited for the handling of panels, which are very flexible and tend to be heavy.