
The resistance heating method adopts a PTC heater, which has strong bonding force, excellent heat conduction and heat dissipation performance, high efficiency, safety and reliability. The PTC heater has the advantages of small thermal resistance and high heat exchange efficiency, and is an automatic constant temperature and power saving electric heater. Its outstanding feature is the safety performance, that is, when the fan fails to rotate, the PTC heater will automatically drop sharply due to insufficient heat dissipation, and the surface temperature of the heater will remain at the Curie temperature ( Generally, it is above and below 250 ° C), so that the surface of the electric heating tube heater is not "reddened".
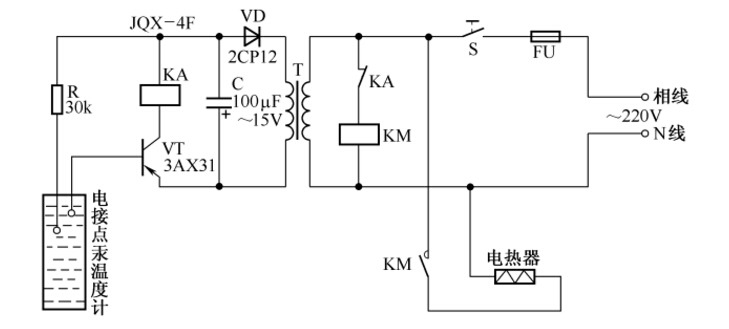
Compared with the PTC heater, the resistance heating element obtained by the method is basically not affected by temperature, and is convenient for precisely controlling the heating temperature and the heating power. The electric resistance heating layer material is atomized into a powder, sieved and dried, and then subjected to laser cladding and/or 3D printing deposition to form a serpentine pattern, and finally the conductive lead is welded, that is, the electric resistance heating element is obtained.
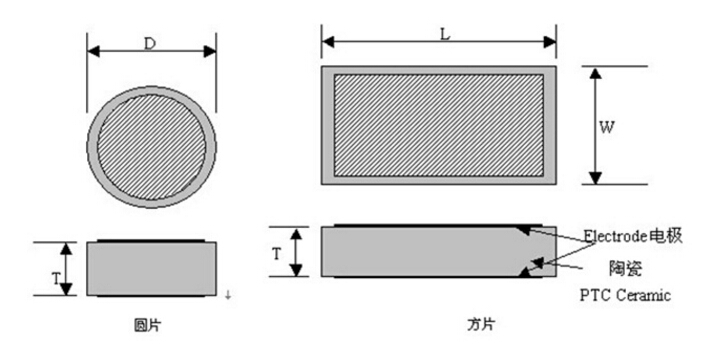
At present, many methods of resistance heating are used in this method. This method is applicable to a wide range of materials, and can be used to form a resistance heating layer on metal, ceramic, glass, and plastic substrates, and has a good application prospect of resistance heating in the market.