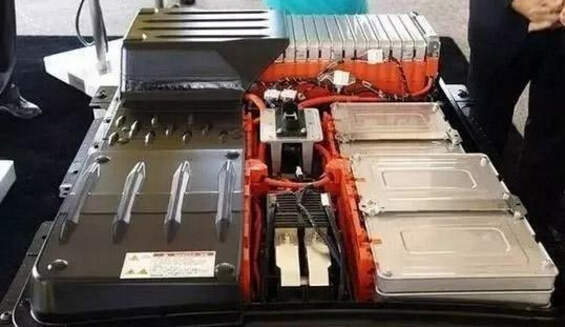
Many automotive resistors use an etched alloy foil resistor structure with a thickness between 20 and 150 mm, so heat dissipation from the resistor material to the terminals is not possible. One of the current solutions is to bond a resistive alloy foil to a substrate material (copper or aluminum) that also has good thermal conductivity with a thin, thermally conductive adhesive. This structure can effectively transfer heat to the surrounding environment, ensuring that the resistor has a very low thermal internal resistance, usually between 10-30K/W, which can effectively cope with the problem of instantaneous high load power heating of automotive electronics.
This resistor structure can work at full load at very high temperatures, and power reduction occurs when the temperature reaches a certain height; at the same time, the temperature of the resistive material can be maintained at a low level. This can effectively improve the long-term stability of the resistor and the change in resistance due to temperature. For new energy vehicles, these effectively improve the safe use of automobiles.
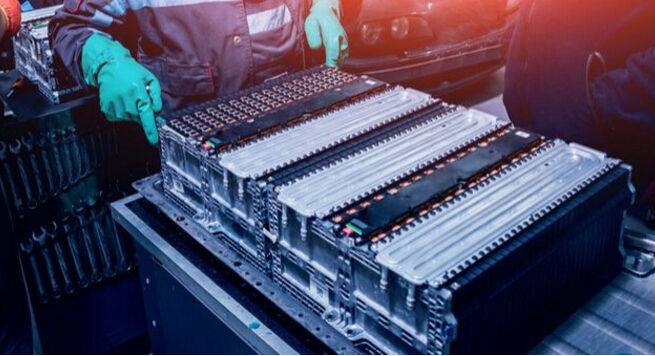
For a very low resistance resistor using a composite structure, the cross-sectional area and mechanical strength of the resistance alloy are large, so it is not necessary to use the bottom plate, which means that the resistance material has a sufficiently low thermal internal resistance, for example, the resistance of 1 milliohms has a thermal internal resistance of about 10K/W, but with a resistance of 100 microohms, the thermal internal resistance is only 1K/W. This new resistor material provides more solutions for working in a new energy vehicle environment, and can bring more choices to automotive electronic systems.