Position:Home » Industry News
Film Resistors' Role in Automotives' Signal Conditioning and Calibration
Writer:Microhm Page View:Date:2020-01-02
In almost all new vehicles, an electronic engine control module teams with sensors and actuators to constitute the engine control system where film resistors play important roles. Piezoresistive transducers implanted in a silicon wafer with bulk micromachined diaphragms have become the dominant technology for producing automotive pressure sensors. Initially an absolute, bulk micromachined, piezoresistive pressure sensor element with a backside constraint for the formation of a vacuum reference cavity--a necessary element for MAP/BAP applications--emerged as the most popular configuration. Lately, however, gauge and differential configurations, as well as configurations where a backside constraint is added for a stress relief only, have evolved to significant production volumes.
Silicon micromachined pressure sensor elements exhibit wide variation of their parameters from part to part, as well as over temperature. To produce a truly interchangeable module for vehicle manufacturers, sensor developers must individually calibrate and temperature-compensate each sensor.
The usual method is to use some sort of adjustment (trimming) within the signal conditioning circuit. The manufacturing and assembly methods and the finished sensor module's electrical performance requirements help determine how the signal conditioning circuit is implemented. Integration technology for this circuit--CMOS, BiCMOS, or bipolar--depends primarily on the selected trimming technique.
At first, automotive piezoresistive pressure sensors contained analog signal conditioning circuits, built using off-the-shelf, packaged, bipolar ICs that were mounted on a PCB. All the necessary adjustments were done using laser trimming of the thick film resistor network that was deposited on a ceramic substrate and then inserted into the PC board in the form of a trim-pack. NRC series and LMK series of Micorhm Electronics are produced in this way. Subsequent advances in hybrid circuit technology permitted both fabrication of the ceramic substrate containing printed thick film resistors and mounting of the signal conditioning ICs in either packaged or bare-die form. These sensor modules became compact, and significant volumes of them are still in production. This mature manufacturing process provides cost-effective sensor modules for applications with moderate size requirements, where thick film resistor stability and accuracy are adequate.
The automotive industry's constant drive for low-cost components, however, forced higher levels of integration to minimize the component count and assembly cost of pressure sensor modules. As a result, analog active circuits were integrated on the same chip with passive, thin film trimmable resistors. By doing this, manufacturers dramatically reduced sensor module sizes and improved sensor performance, primarily because of the thin film resistor's superior stability, as is the case with NAP series and NR series from Microhm Electronics.
Integration of that type has created two-chip solutions, with the sensing element as one chip and the IC with thin film resistors as the other. Monolithic (single-chip) solutions, in which the sensing element, active circuit, and thin film resistors are integrated on one silicon die, are also used in volume production.
All of the above signal conditioning circuits are analog in nature, and the laser trimming adjustments are assumed to be continuous.
Silicon micromachined pressure sensor elements exhibit wide variation of their parameters from part to part, as well as over temperature. To produce a truly interchangeable module for vehicle manufacturers, sensor developers must individually calibrate and temperature-compensate each sensor.
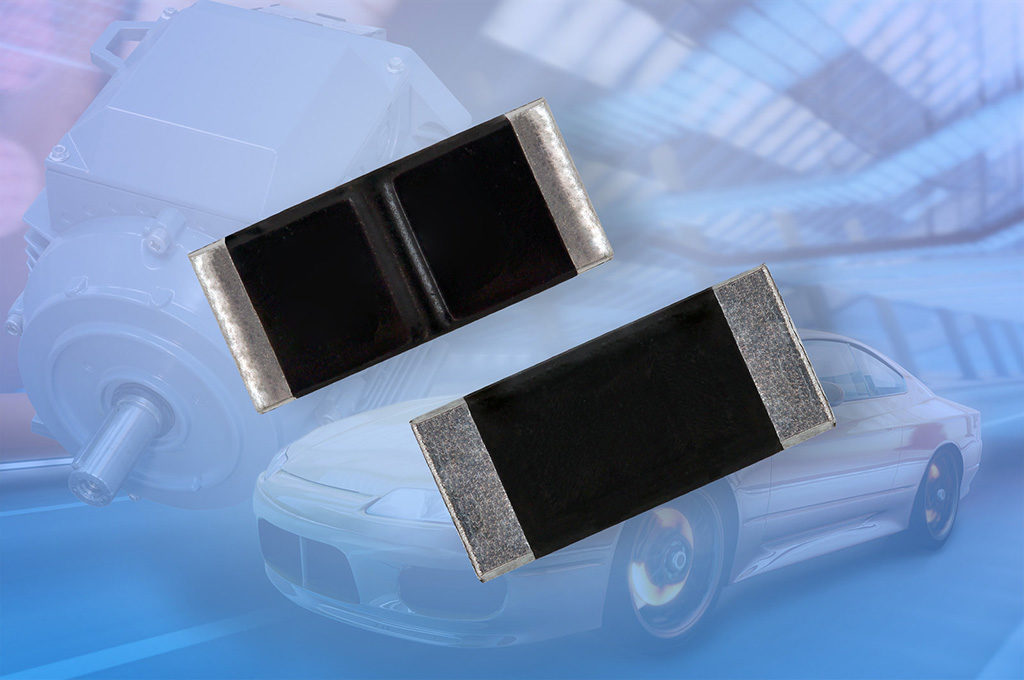
The usual method is to use some sort of adjustment (trimming) within the signal conditioning circuit. The manufacturing and assembly methods and the finished sensor module's electrical performance requirements help determine how the signal conditioning circuit is implemented. Integration technology for this circuit--CMOS, BiCMOS, or bipolar--depends primarily on the selected trimming technique.
At first, automotive piezoresistive pressure sensors contained analog signal conditioning circuits, built using off-the-shelf, packaged, bipolar ICs that were mounted on a PCB. All the necessary adjustments were done using laser trimming of the thick film resistor network that was deposited on a ceramic substrate and then inserted into the PC board in the form of a trim-pack. NRC series and LMK series of Micorhm Electronics are produced in this way. Subsequent advances in hybrid circuit technology permitted both fabrication of the ceramic substrate containing printed thick film resistors and mounting of the signal conditioning ICs in either packaged or bare-die form. These sensor modules became compact, and significant volumes of them are still in production. This mature manufacturing process provides cost-effective sensor modules for applications with moderate size requirements, where thick film resistor stability and accuracy are adequate.
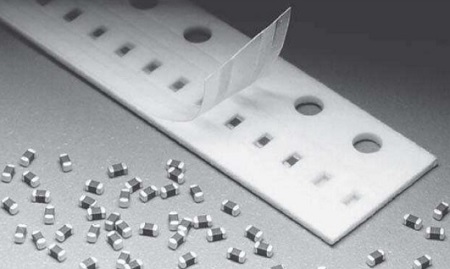
The automotive industry's constant drive for low-cost components, however, forced higher levels of integration to minimize the component count and assembly cost of pressure sensor modules. As a result, analog active circuits were integrated on the same chip with passive, thin film trimmable resistors. By doing this, manufacturers dramatically reduced sensor module sizes and improved sensor performance, primarily because of the thin film resistor's superior stability, as is the case with NAP series and NR series from Microhm Electronics.
Integration of that type has created two-chip solutions, with the sensing element as one chip and the IC with thin film resistors as the other. Monolithic (single-chip) solutions, in which the sensing element, active circuit, and thin film resistors are integrated on one silicon die, are also used in volume production.
All of the above signal conditioning circuits are analog in nature, and the laser trimming adjustments are assumed to be continuous.
Keywords:Film Resisto
Latest News
- Resistor's role in measuring and correcting LED,,,
- Single through-hole resistors' characteristics ,,,
- Why shunt resistors for current sense applicati,,,
- Metal-film resistors with small size, high resi,,,
- 36W High-Current Shunt Resistors MMS8420,,,
- 1W Surface Mount Resistor MPR1206,,,
- An Overview of Microhm Electronics' Resistor Pr,,,
- More anti-sulfur resistors used in harsh envir,,,
- Resistance changes with temperature,,,
- 140W TO247 High Power Heatsinkable Resistor,,,
- MMS5930 is ideal for current sensing in industr,,,
- Shunt resistors selection for engineers' design,,,
- Considerations for choosing precision resistors,,,
- Ceramic Encased Cement Resistors NWH Series for,,,
- Resistors for Passive Balancing in Battery-Pow,,,
Hot Articles
- Microhm will take part in 10th Automotive World,,,
- Thanks for Visiting Microhm's Booth E5-5706 in ,,,
- Resistors in Short Supply: Blame Cars,,,
- New lunch: High Power Precision Shunt Resistor,,,,
- How to Test a Resistor,,,
- Innovative Technology, Future Electric: Electri,,,
- What is Precision Resistors?,,,
- SMD Resistors Sizes and Packages,,,
- The Construction and Features of Metal Film Res,,,
- What is a TO-220 Resisor?,,,
- Hot Selling Products: Precision Shunt Resistors,,,
- How to Calculate the Equivalent Resistance Valu,,,
- What is a Fixed Resistor?,,,
- Resistors in LED Circuits,,,
- Resistors Types and Materials Overview,,,
Resistance applications
- The Measurement Accuracy of Automotive Shunt is,,,
- Shunt Resistor MMS8420 for High Current Stable ,,,
- Urbanization Development Bringing the Transform,,,
- The Four Important Functions of Alloy Resistors,,,
- Heater Blower Motor Resistor in Air Conditioner,,,
- Miniature future for passive electronic compone,,,
- The Main Application for High Precision and Low,,,
- Industrial Roberts Applied to Solar Photovoltai,,,
- Surface Mount Resistor's Size and Package ,,,
- Select the Right Resistor for Harmonic Filterin,,,
- Difference Between High Precision Resistors and,,,
- BMS for New Energy Vehicle,,,
- Why Zero-Ohm Resistors?,,,
- Precision Resistors' Construction and TCR,,,
- Carbon Film Resistors' Features and Application,,,