First, let’s consider the cables which are connecting the device to be measured to the instrument: If you’re measuring resistance near to the source, you’ll get different readings than when you’re taking measurements from a sensor placed 200 ft away. As an example, say we have a resistor which we want to measure. We must connect to it somehow, so we connect a wire to a 1-ohm resistor. But the wire isn’t a perfect conductor either—it has some resistance in it too, as with any piece of wire. If this resistance is 1 ohm per 100 ft. (typical for 20-gauge wire), and we have 3 ft. of cabling going to the device and coming back (6 ft. total) we may expect to see a resistance reading of 1 ohm, but what we’ll see is a reading of 1.06 ohms.
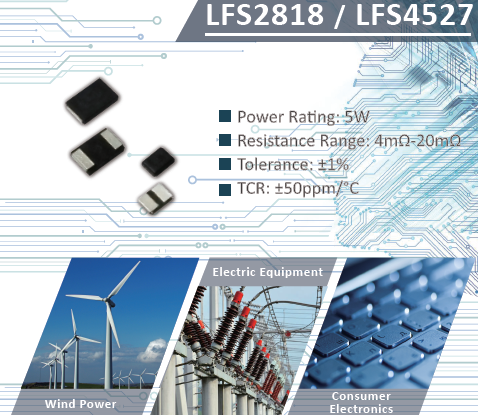
When measuring small resistances, a common technique is to force a known current and then measure the voltage across the Device Under Test. This is following Ohm’s Law since you’re using the current and voltage to determine the resistance. Let’s assume you have a precision current source (for example of 2 milliamps or 200 microamps), and you’ve got a highly accurate voltmeter.
You run 2 wires on either side of the resistor, then force the current through both sets of leads. However, this creates an error in your measurements because the voltage measured at the end of the leads isn’t the same as the voltage across the resistor, as it also includes the voltage drop across the wires between the meter and DUT. Therefore, in this case, you can reduce the error by taking a 4-wire measurement where you use one set of leads to carry the sourced current and a second set of leads which is only used to measure the voltage that you see across the resistor. Microhm Electronics' MVR2321-4 is a typical 4-terminal kalvin resistors which can also be used to measure low resistance by 4-wire measurement. This method provides a much more accurate result by getting around the additional voltage drop caused by the current source through the leads. In this case, it is assumed that the voltmeter draws negligible current which is usually not a problem.
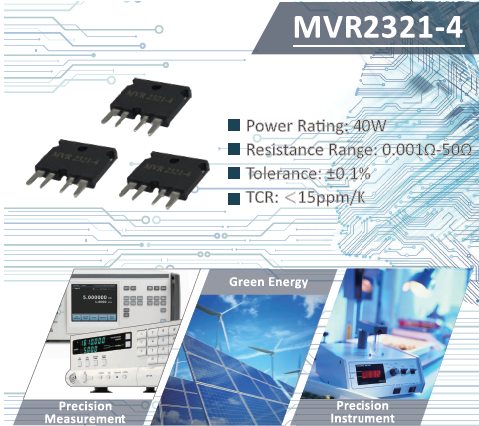
Data loggers can take 4-wire measurements for RTDs or other sensors. These devices both force a current through one pair of wires and then measure the voltage through the other pair of wires. However, there is a limit to how large a resistance you can measure. For example, at the 10,000-ohm range, the smallest current the data logger can force is 200μamps which results in a voltage of 2 volts; at higher resistances (say 1 million ohms) this same current would result in a voltage of 200 volts which is way beyond the capabilities of the loggers. You can’t use 4-wire measurements to measure high resistances with these types of data loggers because you need to either source a very small current or measure a large voltage.
For low resistance measurements, it is possible to use an alternative to the 4-wire measurement by eliminating one of the conductors and performing a 3-wire measurement. In this technique, you measure two voltages: the voltage across the resistor as well as the voltage across the conductor that carries the test current. After taking these measurements, you can determine the error due to the voltage drop in one of the leads. When you’ve determined the error, simply double it and subtract it from your measurements to get a more accurate reading.