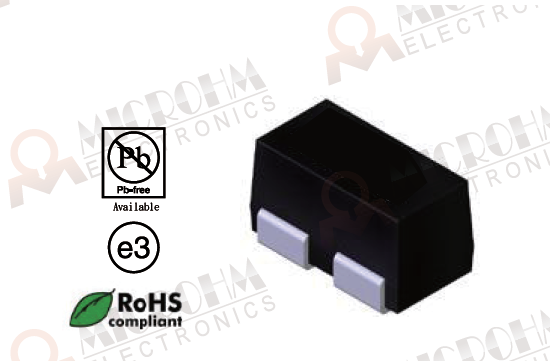
There are certain important manufacturing factors that affect wirewound resistor properties. For example, the wire is wound under tension around a core, which can elongate the wire and alter its diameter. In addition, during formation of the coil, each turn of wire has the inside surface under compression and the outside surface under tension. These deformations are permanent and irreversible. They affect stability and unpredictably shift the TCR from its original value. Over long periods, the wound element tends to change physically as the wire attempts to regain its original shape.
Permanent mechanical changes, which occur randomly and in unpredictable ways, cause equally random and unpredictable changes in the wire’s electrical parameters. Therefore, after winding, resistance elements can have highly variable electrical performance characteristics ranging from excellent to poor.
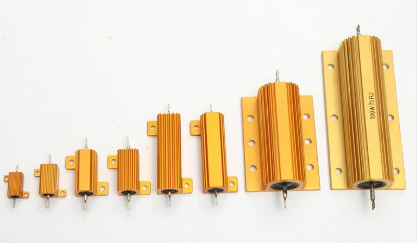
Wirewound resistors have relatively high inductance values due to their coiled-wire construction. There is also an intercoil capacitance. These units thus exhibit poor high-frequency characteristics, especially above 50 kHz. Microhm Electronics have various wirewound resistors, such as NUAL series, EE series and more.
It is difficult to make two wirewound resistors of equal value that can accurately track each other over a specified temperature range. Such tracking is of great importance in high-precision circuitry.
Traditional wirewound manufacturing methods do not isolate the resistive element from the various stresses arising out of handling, packaging, insertion pressures, and lead forming, for example. Here, one must consider tension applied to axial leads on mounting and pressure on the package exerted by mechanically induced forces.