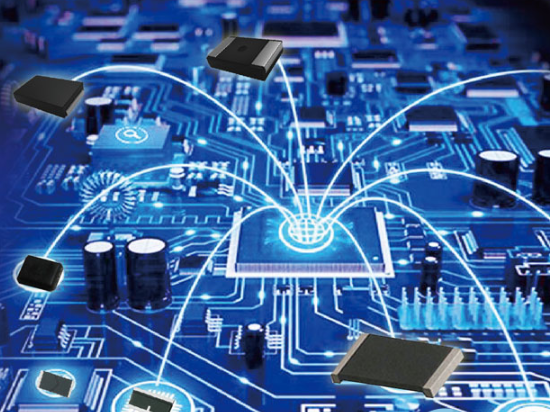
This method is perfectly fine for a power-good indicator LED or any situation where a single low power LED is used. If you do this with LEDs in parallel, the trials begin. LEDs and resistors have their values given within a range, not as absolutes. The cheap, common value resistors you would likely use in a design are typically +/-10%, meaning a 100 ohm resistor could really be any value between 90 ohms and 110 ohms. The forward voltage of a given LED is also a range. LEDs are sorted into groups called “bins” based on their specific color and voltage measurements after production. Depending on how tightly binned you get your LEDs (tighter binning is more expensive), you could see as much as half a volt difference from one LED to the next.
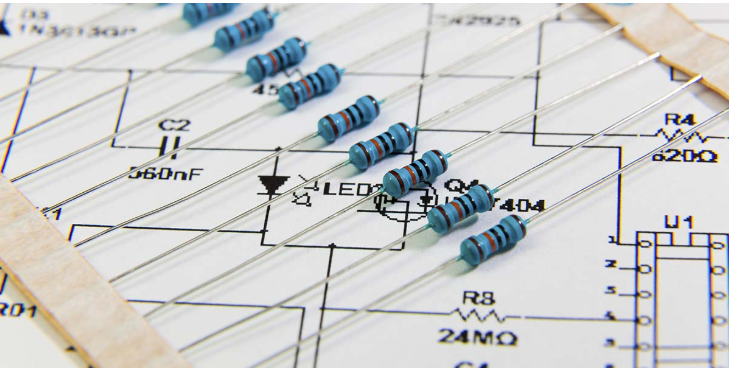
None of these variances are enough to cause trouble in a single-LED situation. If there is nothing to compare to, our eyes will not notice that an extra few milliamps are flowing through a lone indication LED. However, our eyes will absolutely notice brightness variations in a fixture with several LEDs or strands of LEDs running in parallel. Get a string of lower-voltage LEDs next to one with higher voltages and you will definitely see a difference. It is not impossible to get highly precise resistors and mate the correct resistor to each individual strand of LEDs, but this is not practical on any sort of scale and will be both expensive and time consuming. Microhm Electronics PMRY series is an ideal solution.
This is where designers turn to current regulating devices. When multiple strands must be run in parallel due to voltage constraints, the best solution is often to place a small constant current device in series with each string to ensure all strands are performing equally. These devices can be as small as a power resistor and cheaper than high-precision resistors.