For precision use, several technologies - thick film, thin film, foil, and wirewound - are available, offering tradeoffs in performance versus cost. Thick film resistors use a screen printing process to deposit a ruthenium, iridium, for rhenium oxidepaste onto a ceramic substrate. The resistive layer is around 100 microns thick, a thousand times greater than thin film. Although it’s widely used to produce inexpensive, surface-mount components, thick-film technology can also provide higher performance devices (at higher cost, naturally), with tolerances of 0.5 percent. Compared to thin film resistors, thick film technology can handle more power, withstand higher surge conditions, and give resistance values up to 10 TΩ.
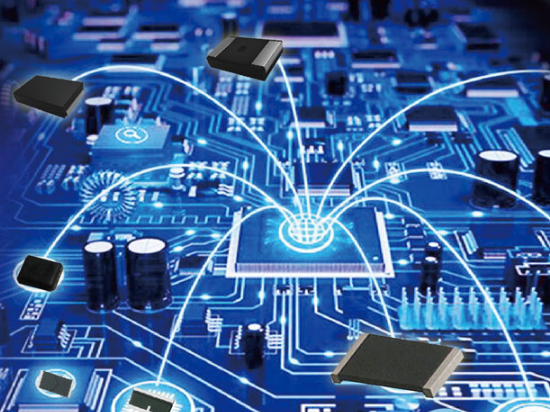
Thin film resistors are made by depositing the resistive material onto an insulating substrate, a vacuum deposition process known as sputtering. This gives a uniform metal film that is much more stable at high frequencies than thick-film types. Resistances up to several MΩ are possible, with tolerances from ±0.05% after trimming and TCR from ±5 ppm/°C, depending on resistance.
Thin-film resistors are also low inductance. By forming the film on a heat-conducting alumina substrate that is metalized and soldered to a heat-dissipating copper plate tab, it’s possible to create low-cost, high-power film resistors in small TO-style packages.
Foil resistors offer the highest overall stability and precision. These use a foil for the resistive element, made of special alloy several microns thick. The foil is bonded to the substrate, then photo-etched into a pattern that contains a series of pre-determined trimming locations. NMS2818, NMS 4527, MVR2321-4, MPR series of Microhm Electronics are popular metal foil resistors in the market.
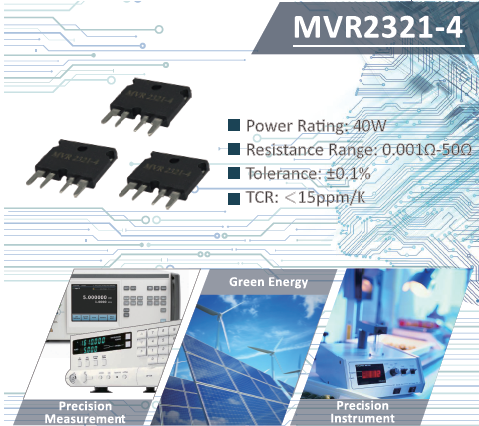
Wire wound resistors, a traditional choice for throughhole applications, consist of a resistive wire wound around a ceramic core. The wire is made from alloys such as Nichrome or MnCu; these have extremely low thermal coefficients of resistance (TCR) and excellent long-term stability.
As a professional resistor manufacture, Microhm Electronics provide precision film resistor, foil resistors, wirewound resistor as well as shunt resistors with competitive prices.