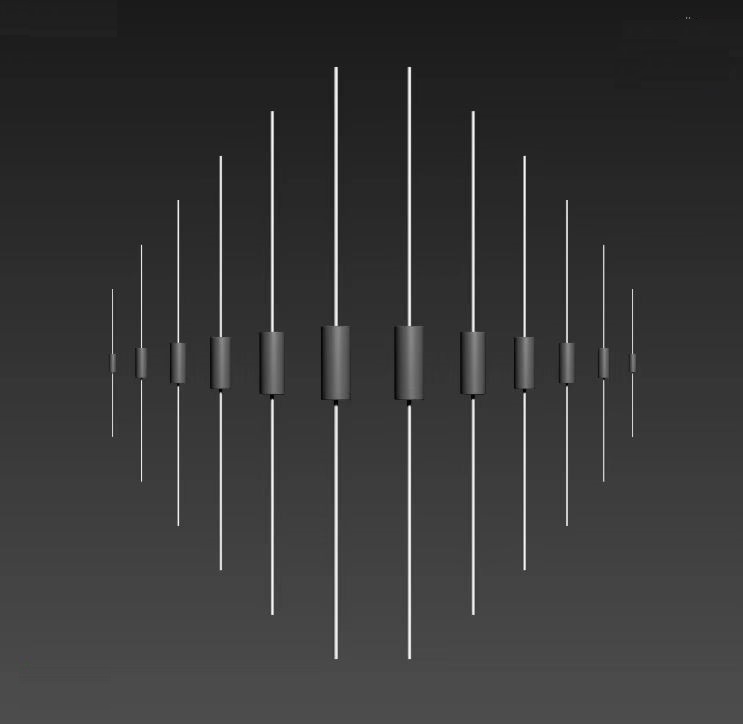
Parts testing may vary depending on the specification’s requirements. However, the tests are usually separated into groups. Some undergo screening tests performed on 100% of a production lot, while other lots undergo destructive tests performed on a sample of units from within a specific lot to guarantee the performance of the rest.
For space-project applications (or even military and avionics), a more specific and relevant testing pattern developed by NASA may be used as a basis. The EEE-INST-002 guidelines titled “Instruction for EEE Parts Selection, Screening, Qualification, and Derating” are used as a basis for the development of several specifications that use foil resistors. Subjecting the resistors to the aforementioned sequence of tests can improve the confidence level of a part to perform in a critical space application. NASA developed the EEE-INST-002 guidelines to be flexible enough to accept any technology and part type. Consequently, there are foil devices with a number of different specifications suitable for these types of critical projects.
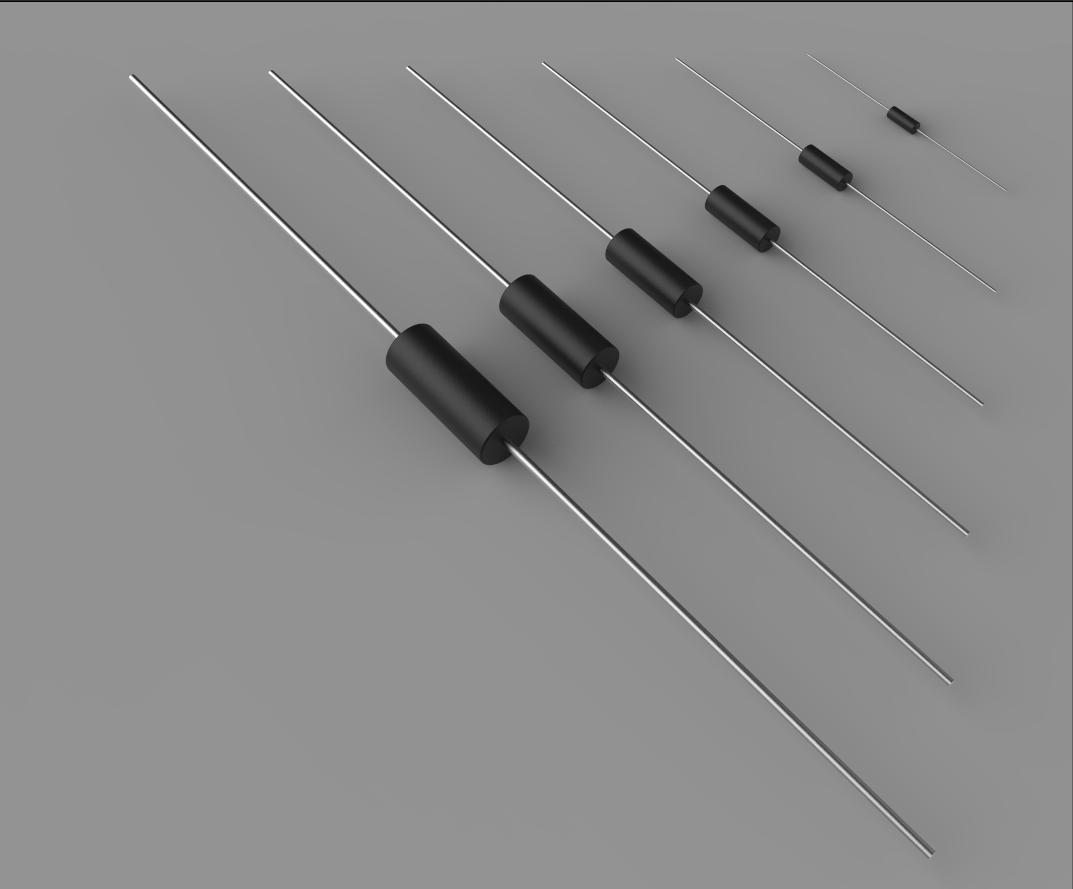
Some military applications require a part that’s not qualified to a QPL specification. The Defense Supply Center of Columbus also maintains several up-screening plans oriented around high-demand products that haven’t been QPL-qualified. These specifications, known as DSCC specs, consist of a 100% screening test (Group A testing) and a destructive series of tests (Group B testing). DSCC specifications are easily recognized by engineers, distributors, and QA organizations and come in a wide variety of part types. Hermetically sealed precision foil-resistor networks are available with screen/test flow in compliance with EEE-INST-002 (Tables 2A and 3A, Film/Foil, Level 1) and MIL-PRF-83401.