Q: A simple but obvious question: what is used as the material for heat sinks?
A: They are usually made of aluminum, but sometimes copper is used. While copper has better thermal conductivity than aluminum, it is heavier, more costly, and cannot be extruded. Aluminum has favorable thermal, fabrication, weight, and other desirable attributes which make the preferred choice over copper in most cases. Microhm high power resistor Nual, LHR and MVR series are also used aluminum heat sink to dissipate heat.
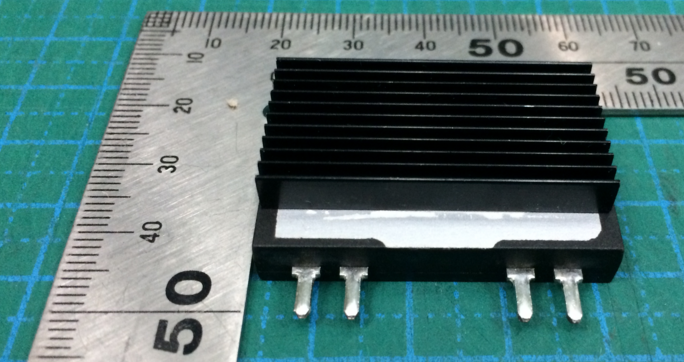
A: The answer, of course, depends on the heat sink style. For most IC heat sinks, there is a flat area which rests in the flat top of the IC or module package to be cooled. The heat sink may be fastened with small screws, a clip, a support strap, or even a single small screw directly to a tab on the component (if it has a thermal tab, as do many including this TO-220 package). Microhm Electronics' high power resistor NLR30 and NLR35 are typical To-220 package resistors with heat sink.
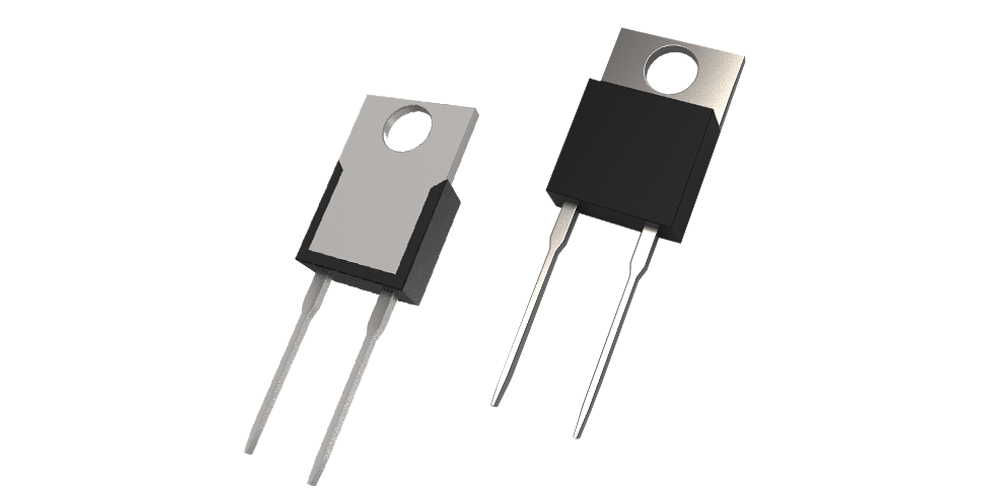
A: No, it requires more than simple placement. The heat sink must be in good thermal contact with the package, which requires an interposed thermal interface. This can be a very thin layer of special non-adhesive paste, or a special elastomeric pad, among other choices. The objective to have as little thermal resistance as possible between the IC or module and the heatsink, without even microscopic voids.
Q: What are the sizes and styles of heat sinks?
A: They can be as small as a fingernail and as large as a chassis in a rack or an entire rack. The most common heat sink is an array of fins or pin; the function of these “obstacles” is to interfere with airflow such that their heat can transfer from its solid surfaces to the surrounding air. These heatsinks are available in countless sizes, with many pin/fin configurations and shapes to meet the somewhat conflicting goals maximizing surface-to-air area while not excessively impeding the critical air flow.
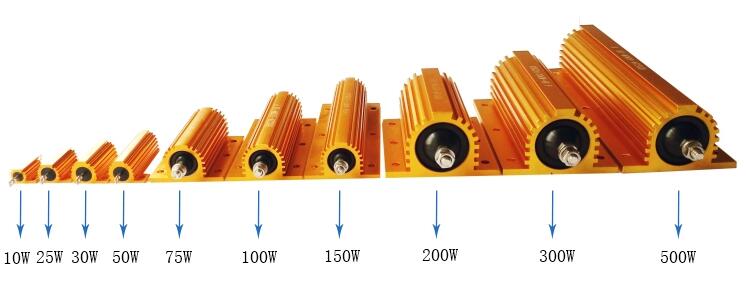
Q: Given the thousands of basic heats available and their many variations, how do you make the choice as as to which how much heat sink is needed and which type? Is this difficult?
A: It used to be, but now, thermal modeling and simulation tools are available from many vendors which it a reasonably straightforward process. Many engineers start with a quick, rough analysis to get a sense of how much heat-sink performance they need and use that as a starting point.
This FAQ has explored some of the many aspects of heat sinks and their role in the thermal management of an IC, board, or module. As with most simple-looking issues, their reality is both simple and complex at the same time. The heat sink is a passive, single-piece component without moving parts, but choosing the right one in terms of function, performance, cost, and size requires consideration and study.